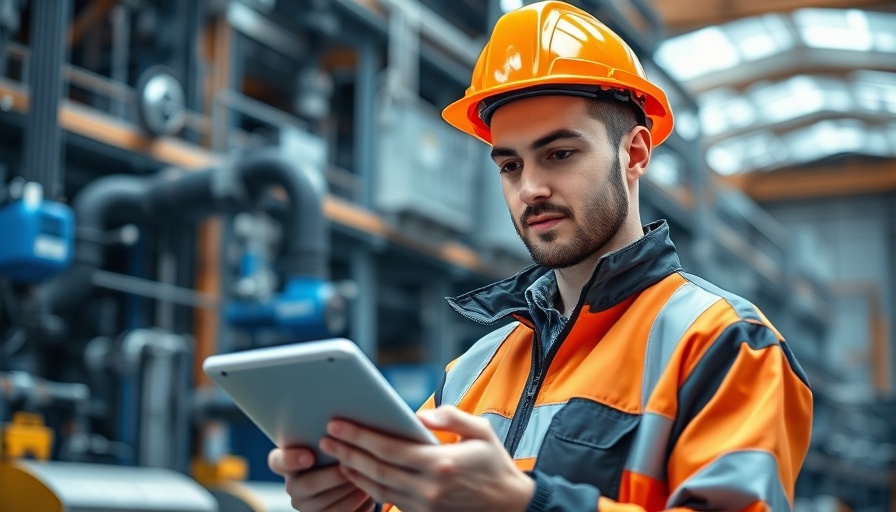
Understanding Digital Twins: The Next Frontier in Manufacturing
As the era of digital transformation unfolds, digital twins emerge as groundbreaking tools that revolutionize the manufacturing sector. A digital twin is not just a replication; it’s a sophisticated model that mirrors real-world objects, systems, or processes through continuous, data-driven updates. Unlike traditional models that use historical data, digital twins leverage real-time sensor input and AI-driven analytics to simulate potential outcomes and optimize performance.
The Role of Digital Twins in Predictive Maintenance
One of the most significant benefits of adopting digital twins lies in predictive maintenance. This innovative approach allows manufacturers to preemptively address potential equipment failures rather than responding to them reactively. By utilizing digital twins, companies can collect valuable data through IoT-generated real-time monitoring and AI analytics to forecast when machinery will need maintenance, effectively minimizing unplanned downtime. For example, in the aviation industry, jet engine digital twins continuously analyze performance metrics, preemptively identifying wear and tear before they lead to failures.
Enhancing Efficiency and Reducing Risks
Digital twins provide manufacturers with an unparalleled advantage in efficiency and risk reduction. By comparing actual production conditions to ideal metrics, manufacturers can swiftly identify and rectify deviations that might hinder output. These virtual models are crucial during the design phase of new products, allowing simulations to optimize assembly lines before physical production even commences. Such practices not only diminish errors and risks but also streamline production timelines, drastically shortening decision-making cycles from years to mere months.
Transitioning from Digital Shadows to Dynamic Twins
Many organizations still depend on digital shadows, which consist of static historical data models lacking predictive capabilities. However, making the shift to fully functional digital twins requires integrating several critical components:
- Continuous, IoT-Generated Streaming Data: This real-time data feeds vital updates, ensuring that digital twins reflect current operational statuses.
- Predictive Analytics and AI: By employing machine learning algorithms, industries can unveil optimization opportunities and foresee potential failures.
- Simulation Data: Leveraging AI- and physics-based simulations enables testing of performance metrics under varied scenarios.
- Service and Historical Data: Analyzing maintenance histories aids in recognizing patterns that inform decision-making.
- Situational Intelligence: Advanced interfaces provide actionable insights to operators, enhancing decision science.
Combining these elements marks the transition from a reactive stance on maintenance to a proactive optimization strategy, allowing companies to greatly enhance asset lifecycle and performance.
The Future of Digital Twins in Manufacturing
The future potential of digital twins in manufacturing is immense, with industries set to become increasingly data-driven. As organizations continue adopting advanced AI technologies and integrate digital twins more deeply into their operations, they will not only improve performance and efficiency but also unlock new avenues for innovation. This transformation fosters an ecosystem where predictive maintenance is the norm rather than the exception, pushing industries towards completed operational agility.
Taking Action in the Age of Digital Twins
Understanding the value of AI learning pathways in relation to digital twins can be beneficial for professionals engaging with these technologies. Companies should consider investing in AI science and analytics to harness the full potential of digital twins. As we navigate through rapid advancements in technology, taking steps now by leveraging digital twin capabilities can yield substantial competitive advantages.
For those interested in diving deeper into the world of AI and its relevant applications, pursuing a curated learning path is recommended. This knowledge not only enhances personal expertise but also ensures active participation in the ongoing industrial revolution.
Write A Comment